R
AUTOMOTIVE COOLING COMPONENTS

Up to the 1980s, radiator cores were often made of copper (for fins) and brass (for tubes, headers, and side-plates, while tanks could also be made of brass or of plastic, often a polyamide). Starting in the 1970s, use of aluminium increased, eventually taking over the vast majority of vehicular radiator applications.Copper-brass conducts heat considerably better than aluminum does. Bigger tubes and more fins increase surface area. ... The compromise comes from building the tubes out of aluminum. An aluminum radiator using 1-inch-wide tubes with 0.016-inch wall thickness is 60 percent lighter than the same copper-brass
Over the next few years, new copper-brass car and truck radiators that could last ten years will debut in the automotive industry. They are fully competitive with today's aluminum counterparts.
Based on technological advances and design innovations developed with research funding from the International Copper Association (ICA), these radiators are 35%-40% lower in weight compared to traditional, nonoptimized copper-brass radiators, and correspondingly lower in material costs.
They have lower weight because they are manufactured with far less material in their fins and tubes than previous models, and because the heavy lead-base solder traditionally used in copper-brass radiators is replaced with a very small amount of light brazing alloy.
The brazed copperbrass radiators also provide 30% or more lower air side pressure drop than aluminum radiators because their copper and brass components are much thinner than the components in their aluminum counterparts.
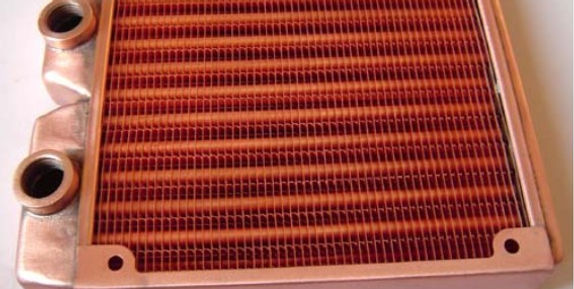